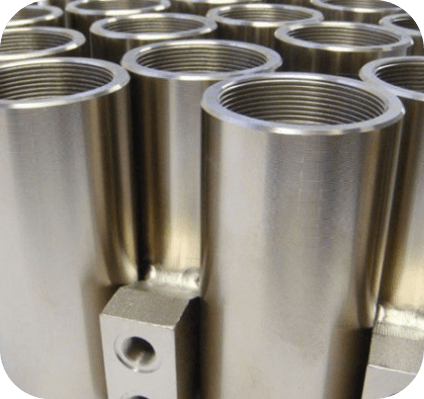
The electroless nickel plating added to a metal surface follows an autocatalytic chemical reduction. This process doesn’t use an outside source of electricity. In electroplating, phosphorous or nickel is deposited on the metallic surface using a chemical bath. Non-conductive surfaces can be plated with electroless nickel-coated surfaces. With this electroplating process, high-precision parts are coated uniformly on ferrous and non-ferrous surfaces to improve their corrosion resistance. AMS 2404E, AMS 2404B, and Mil-C-26074E are a few of the industry standards that we comply with at FMC.
FMC provides a broad range of electroless nickel coatings, as per the application needs, including small and large components. We can Electroless Nickel Plating in Dubai and enp challenges and deliver perfect results at the most competitive prices. Our facilities and experience are crucial in delivering a premium-quality product cost-effectively. The benefits of electroless nickel plating include friction resistance, wear or corrosion resistance, and uniformity in the coating.
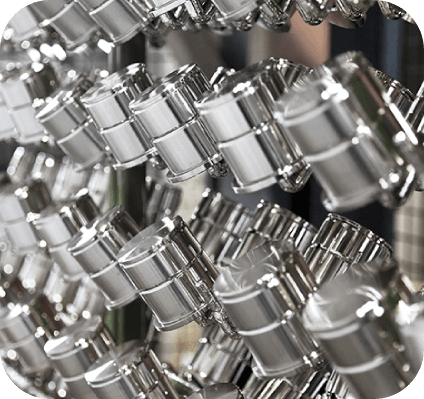
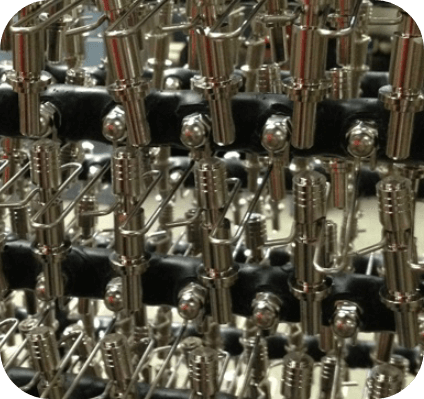
The commonly used electroless nickel coating contains MPEN, also known as medium levels of phosphorus. MPEN generally ranges anywhere between 5% and 9% of phosphorus. Processes that use this type of electroless nickel have high-speed deposit rates and semi-bright and bright options. The low phosphorus electroless nickel that’s under 5% phosphorus provides configurations and parts with a uniform thickness and has alkaline corrosion resistance. A high level of corrosion resistance is needed in coal mining, oil drilling, and other applications that require electroless nickel because of its high phosphorus content. Get in touch with FMC to get top-of-the-line electroless nickel plating at competitive prices!
Standards Followed In FMC
ASTM B733 – Autocatalytic (Electroless) Nickel-Phosphorus Coatings on Metal