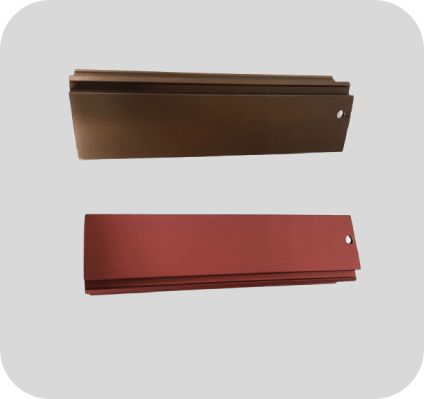
By electrochemically treating metal surfaces, anodizing forms corrosion-resistant, durable oxide finishes that are decorative and corrosion-resistant.One of the perfect and best-suited metals can be aluminium, while other metals like titanium and magnesium can also be anodized. The anodizing parameters used in FMC are voltage, time, current density, electrolyte composition, temperature, pre-treatment, and anodizing regime. When tweaking these parameters, the properties of materials that can be modified by anodizing are color, hardness, thickness, porosity, biocompatibility, and corrosion resistance.
As a result of FMC anodizing, a part will maintain its cosmetic appearance in all conditions, despite prolonged wear and tear and corrosion.Chromic acid anodizing, sulfuric acid anodizing, and hard coating are some common types of anodizing.
The anodic oxide structure of the aluminium substrate is wholly composed of aluminium oxide. The aluminium oxide cannot be applied like plating or painting to the surface, but it’ll be completely integrated with the aluminium substrate, so it doesn’t peel or chip. They have a porous structure, allowing secondary processes like sealing and colouring.
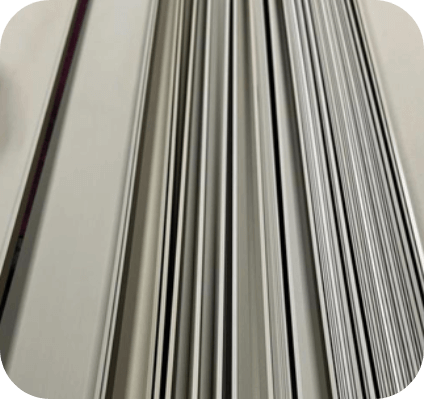
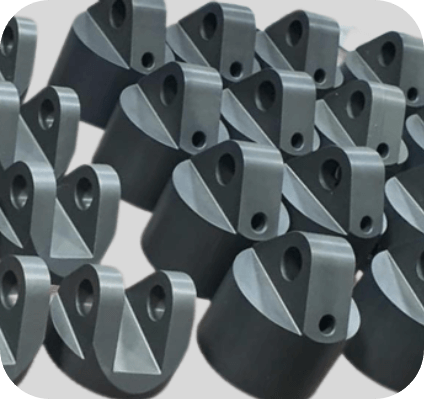
In anodizing, the aluminium is immersed in an electrolyte bath and passed over an electric current. The aluminium serves as an anode, and the cathode gets mounted inside the anodizing tank.At the surface (the part where it gets anodized), oxygen ions come out of the electrolyte and combine with aluminium atoms. As per the thickness, the anodized coatings come in at around 8–16 μm or up to 50 μm for hard coating. The top benefits of the anodizing process are that it is safe to use, cost-efficient, and has no harmful environmental by-products. Contact FMC if you’re looking for an anodizing process for your industry!
Standards Followed In FMC
ASTM: B 253 – Aluminium Surface Preparation
ASTM: B 322 – Degreasing prior to Anodizing
ASTM: B 580 – Anodic Oxide Coatings on Aluminium